Discover how CAMWorks CNC software efficiently programs your CAD Design.Maximize efficiency with our intuitive, feature-based CAM software.
CAM Software - CNC Programming Software for Machine Tools
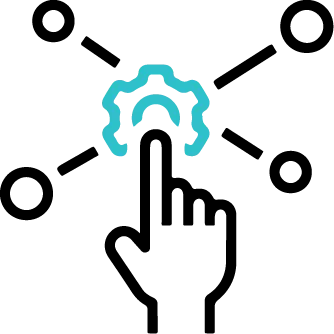
Fully Integrated
Seamlessly integrated and fully associative with SOLIDWORKS and Solid Edge, saving time and reducing errors
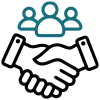
Complete Associativity
CAD and CAM data are saves in one file, and when a design change occurs, operations and toolpaths update automatically
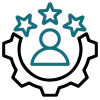
Intelligence-Based
CAMWorks TechDB™ shortens programming time by capturing your best practices for use in other part programs
Why HCL CAMWorks?
Shorten Programming Time
Seamlessly integrated within SOLIDWORKS and Solid Edge, HCL CAMWorks eliminates time-consuming rework caused by design updates. This integration enables:
- Effortless Synchronization - Automatic updates between design and manufacturing
- Reduced Errors - Minimized risk of human error due to manual updates
- Increased Productivity - More time for innovation, less time spent on rework
By integrating with your CAD system, CAMWorks helps you work more efficiently and effectively.
Golden State Innovations
Increase Accuracy and Quality
Advanced technologies in HCL CAMWorks reduce repetitive programming tasks, streamlining your workflow and boosting productivity.
- Automatic Feature Recognition - Instantly identifies machining part features from the CAD model
- Intelligence Based - automatically selects tools, creates operations, and generates toolpaths based on the part features
- Technology Database - captures and re-uses your preferences and best programming practices for use in subsequent part programs
With ideal automation levels, CAMWorks reduces errors and gets your parts to production quicker.
CAMWorks CNC CAM Software Overview
Reduce Machine Cycle Time
HCL CAMWorks utilizes advanced high-performance toolpath generation for rough milling and turning operations to dramatically reduce machine cycle time and increase tool life.
- VoluMill - Generates toolpaths with continuous tangent motion for high-speed machining and reduced machine load
- VoluTurn - Provides smooth toolpaths for turning parts without sharp corners, reducing wear on inserts
- PrimeTurning™ by Sandvik Coromant - Offers the flexibility for turning operations in all directions
Get the most out of your CNC machines with toolpaths that run machines smoother, cooler, and faster.
VoluMill Machining
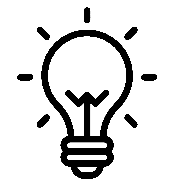
Program Smarter
Reduce programming time by up to 90% with fully integrated CAD/CAM, feature-based programming and automatic feature recognition
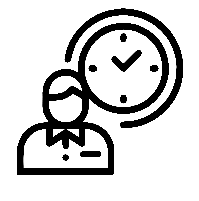
Machine Faster
Decrease cycle time by as much as 85% and increase tool life up to 500%, even in the hardest materials, with revolutionary high speed machining options
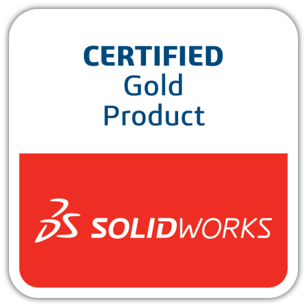
The first SOLIDWORKS Certified Gold Product for CAM Software
Some of Our Customers
From custom job shops to large scale production...
Empowering partnerships through seamless collaboration

Reseller Area
Exclusive place for our Sales Partners / Resellers to access all latest updates / files and information on HCL CAMWorks

Customer Area
Access HCL CAMWorks Dashboard to download software and collateral

Find a Reseller
Access Worldwide Network of Authorized HCL CAMWorks Resellers

CAMWorks® best-in-class CNC programming solution enables users to program smarter and machine faster.