Reduce Cycle Times
CAMWorks® VoluMill™ is an ultra high-performance toolpath engine within CAMWorks for 2.5 axis and 3 axis roughing operations
Improve your Machining Time
CAMWorks® VoluMill™ is an optional ultra high-performance toolpath engine within CAMWorks for 2.5 axis and 3 axis roughing operations.
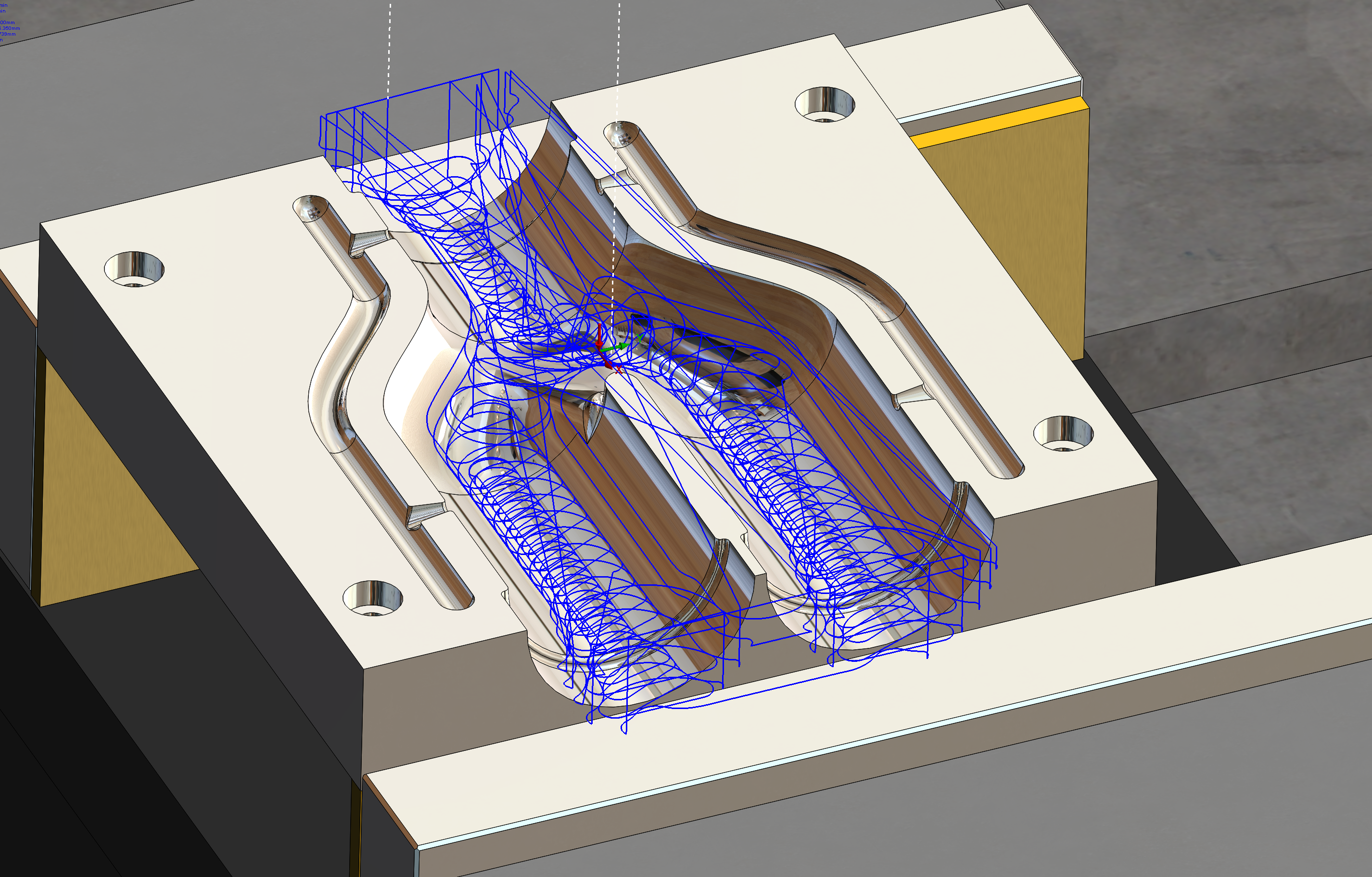
CAMWorks® VoluMill™ is ideal for complex 3-D shapes and prismatic parts as its algorithms result in more intelligent toolpaths to machine pockets, slots, and arbitrary shapes. VoluMill is well suited for machining soft as well as hard materials that are hard to chip, such as titanium, nickel-based alloys or stainless steel. The result is increased efficiency and utilization of machines, tools, labor and materials.
Program Smarter, Machine Faster! The high-performance roughing module, which is fully integrated in CAMWorks, combines optimal milling paths and maximum material removal with minimized machining times. VoluMill’s unique approach to high speed material removal allows the programmer to determine the optimum material removal rate for any combination of part geometry, material, machine, and cutting tool. Material is removed in the most effective way possible. Consequently, machines run smoothly and tools run cooler.
- Reduce your Cycle Times up to 80%
- Reduce your programming times up to 50%
- Increase your Cutting Tool Life up to 500%
Improve customization and setup time...
See CAMWorks Live!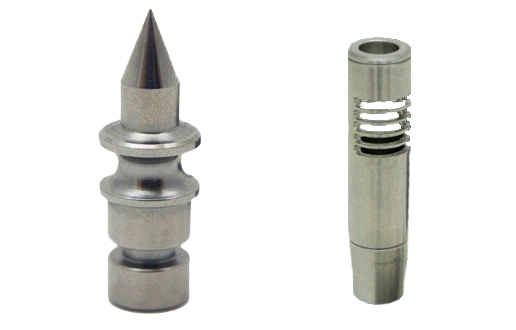
Tomak Precision: A CAMWorks Success Story
“There is no wasted motion. For example, when you calculate an internal corner there is a whole lot of math involved. CAMWorks VoluMill does most of that math for you, saving an average of 50% of machining time for these features.” - Arlie Branham, Tomak Precision
Tomak is a job shop that prides itself on its advanced manufacturing technology and highly skilled individuals. It sees this mix as giving it the edge it needs to serve demanding customers in the aerospace, medical, machine tool and other industries, handling everything from prototype work to short lots to full production runs.

CAMWorks® best-in-class CNC programming solution enables users to program smarter and machine faster.