HCL CAMWorks 2025 is the latest release of HCL CAMWorks – powerful CAM software for CNC programming which is fully integrated with SOLIDWORKS®, 3DEXPERIENCE SOLIDWORKS, and Solid Edge®. CAMWorks 2025 adds functionality in direct response to customer requests, making the software even more powerful and easier to use. Below are some of the many improvements included in CAMWorks 2025.
CAMWorks for 3DEXPERIENCE SOLIDWORKS
- HCL CAMWorks has been officially authorized by Dassault Systèmes to develop, support, and promote add-ins for all SOLIDWORKS applications working with the cloud-based 3DEXPERIENCE platform
- HCL CAMWorks is seamlessly integrated with 3DEXPERIENCE SOLIDWORKS, facilitating the power of data management and cross-discipline collaboration in the cloud
- CAMWorks for 3DEXPERIENCE SOLIDWORKS is fully compatible with the CAMWorks and SOLIDWORKS CAM data from the SOLIDWORKS desktop version
Experience Better and Faster HCL CAMWorks
Machine Aware Programming Extended with Machine Components in Simulation
- Ability to display loaded turrets in full simulation as well as step through simulation
- Supports collision detection to prevent machine downtime and crashes
- Displays the spindle head in milling
- Includes the option to reset the customized simulation machine data in the Machine Definition dialog box back to the original state
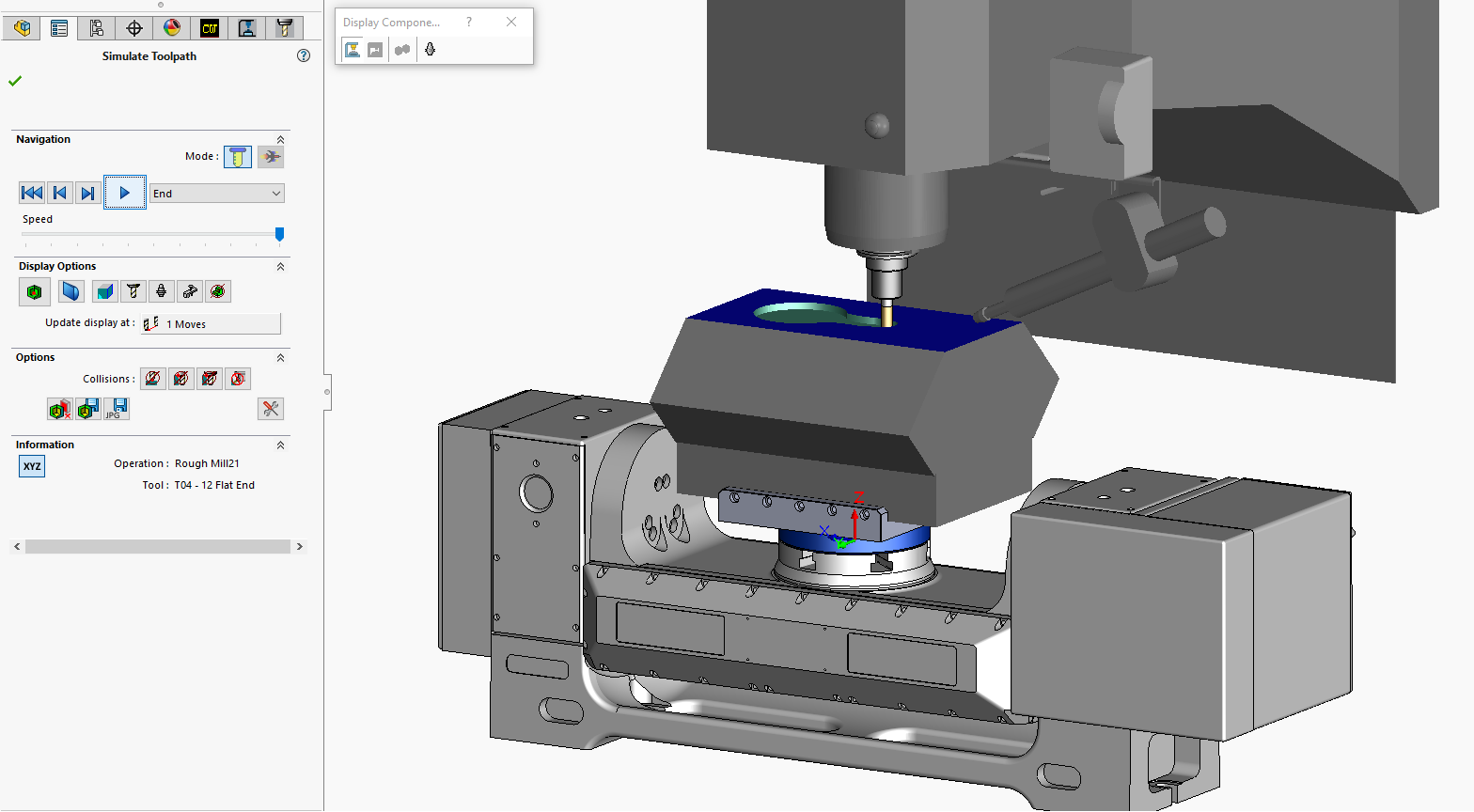
New Options for Automatic Feature Recognition of Turn Features
- Users can control which Turn features are to be recognized with Automatic Feature Recognition, saving time with part programming
- For example, a cutoff feature or face feature can be unchecked so that it is not included when Extract Machinable Features command is executed
- Cutoff feature has bar stock and other stock type options
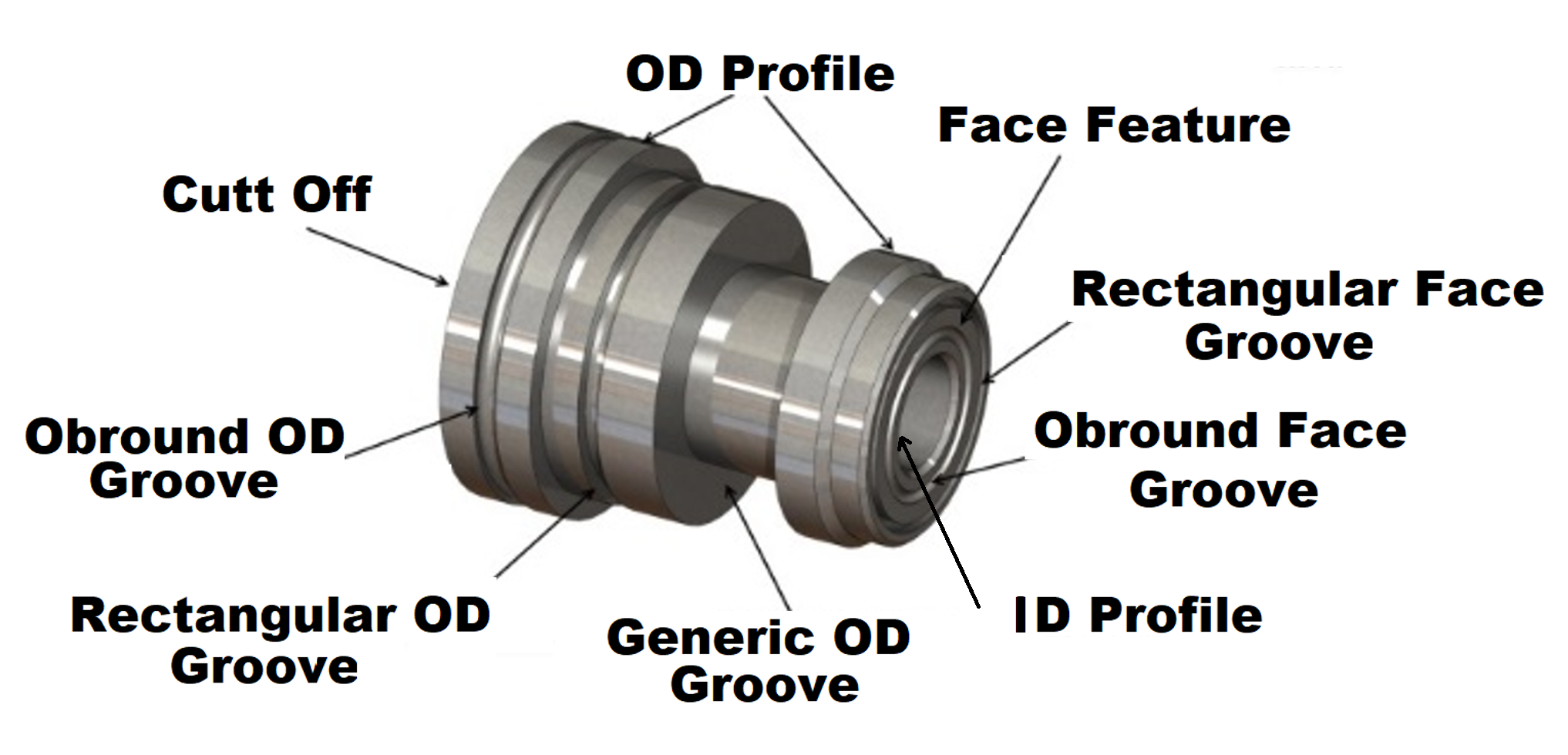
New Sync Manager Turret and Spindle Views
- An expanded view of the Sync Manager provides complete visualization of synchronized operations that includes turret and spindle data
- Enables users to visualize the synchronization of operations by sorting them into columns by the turret or by the spindle-turret combinations, assigned to the tools used for the operations
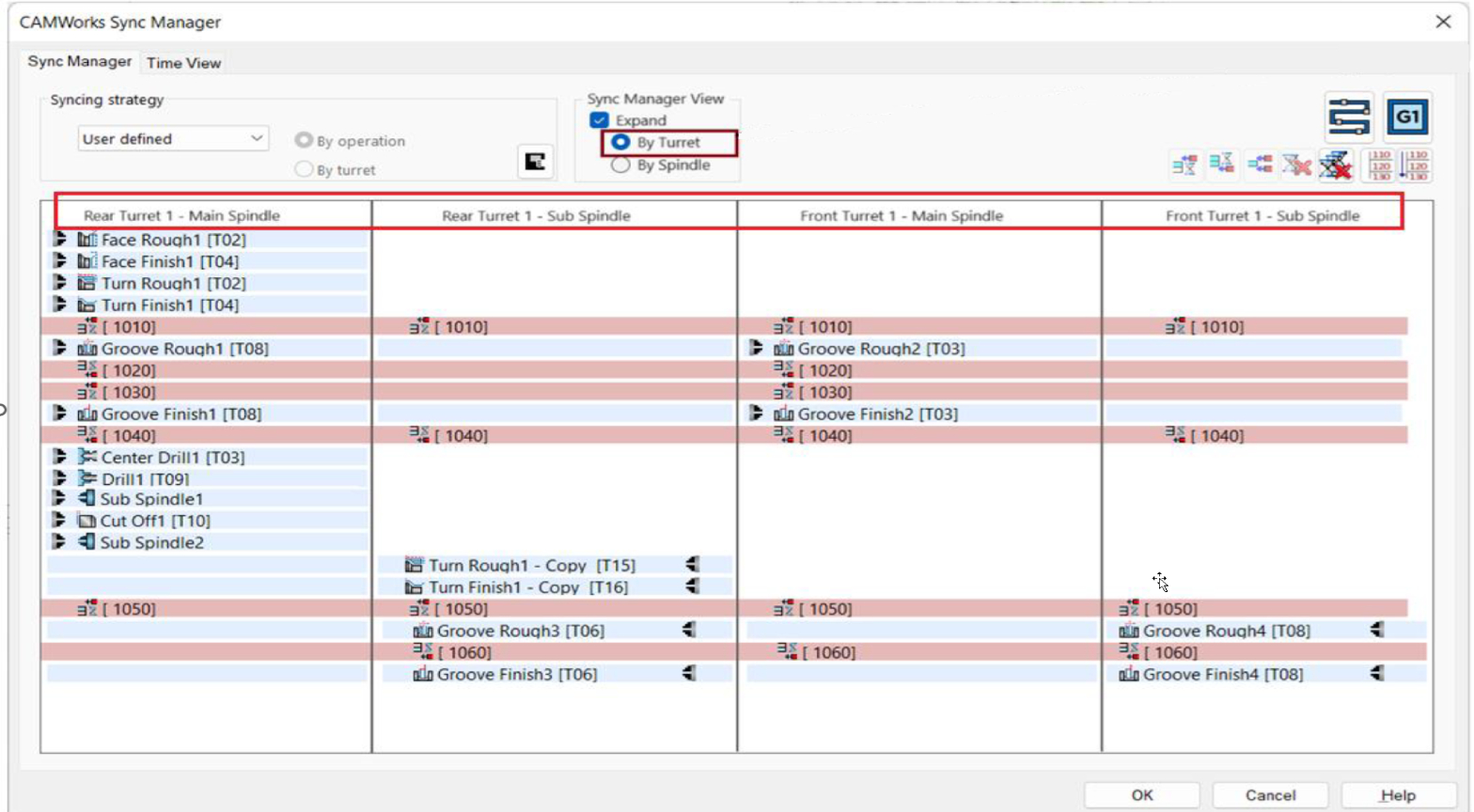
Defining Orientation for Milling Tools
- Ability to define the orientation of milling tools present in mill-turn tool cribs
- Allows unused tools to be shown in the correct orientation
- Options include left, down, right, up, and undefined
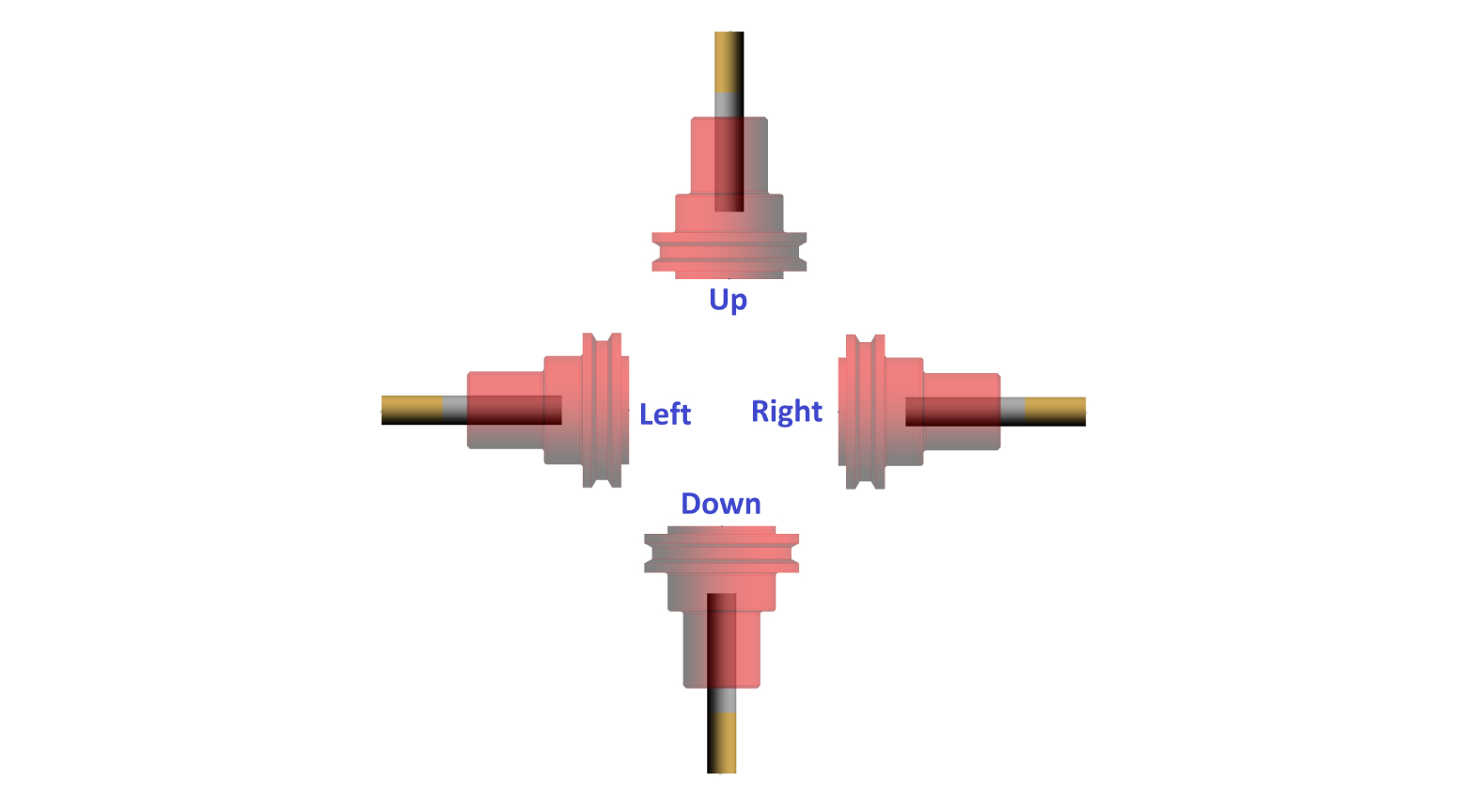
Additional Tools for Deburring and Chamfer Machining
- Option to select a Ball Nose, Hog Nose, or Lollipop tool for deburring and chamfer machining in contour milling operations
- Provides expanded tool options for users with these tool types
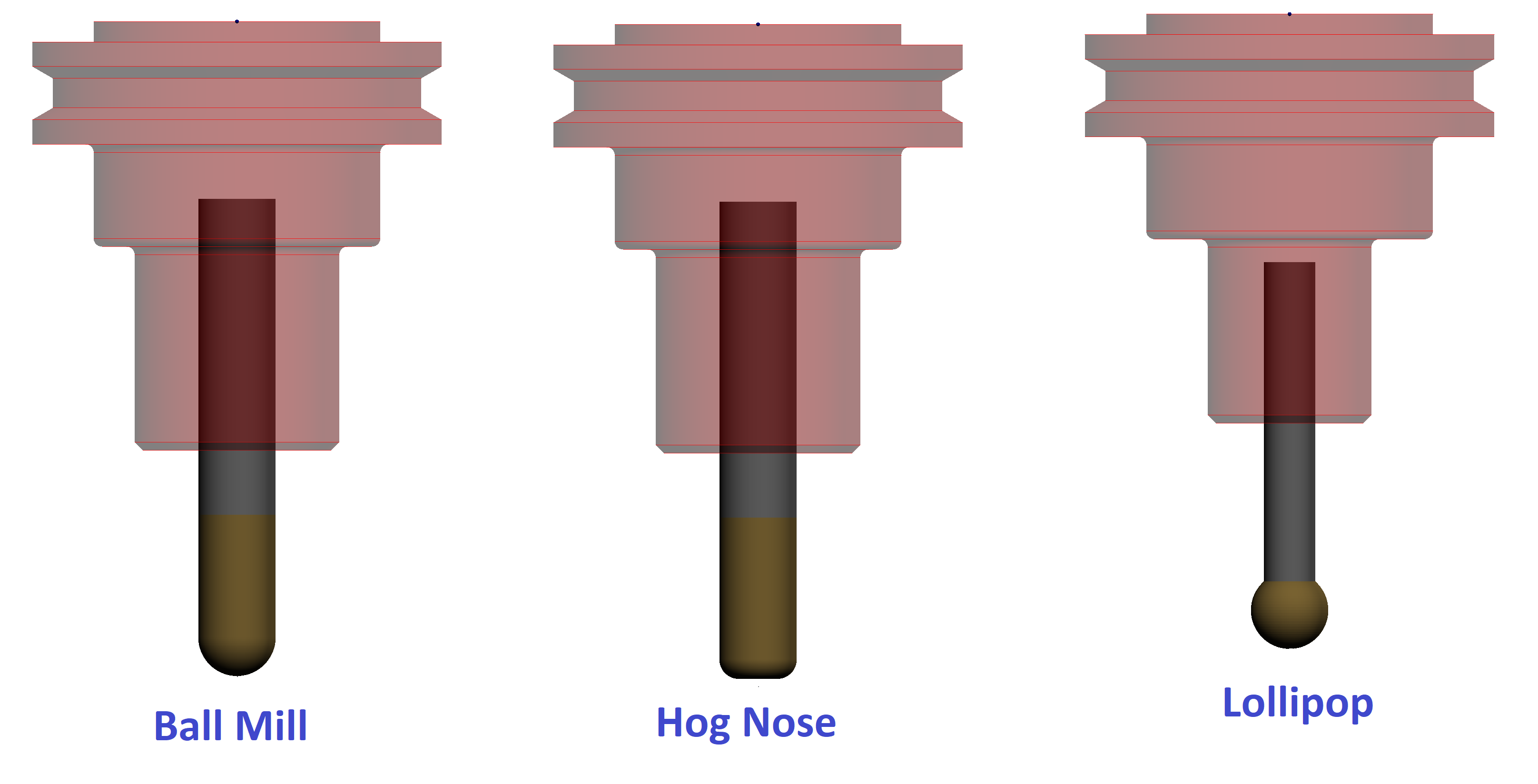
Collets as Work Holding Device
- Option to define a collet as the work holding device on a turn and mill-turn to machine a part model or assembly
- Users can assign a desired collet saved in the TechDB to the turn or mill-turn machine
- Collets are capable of producing a high clamping force and accurate alignment

Bar Break Chamfering Option in Turn
- Support for bar break chamfering of the stock in turn toolpaths to prevent and eliminate burrs that can potentially damage machine components
- Option is available for turn roughing and finishing, groove roughing and finishing of OD feature, and face roughing and finishing
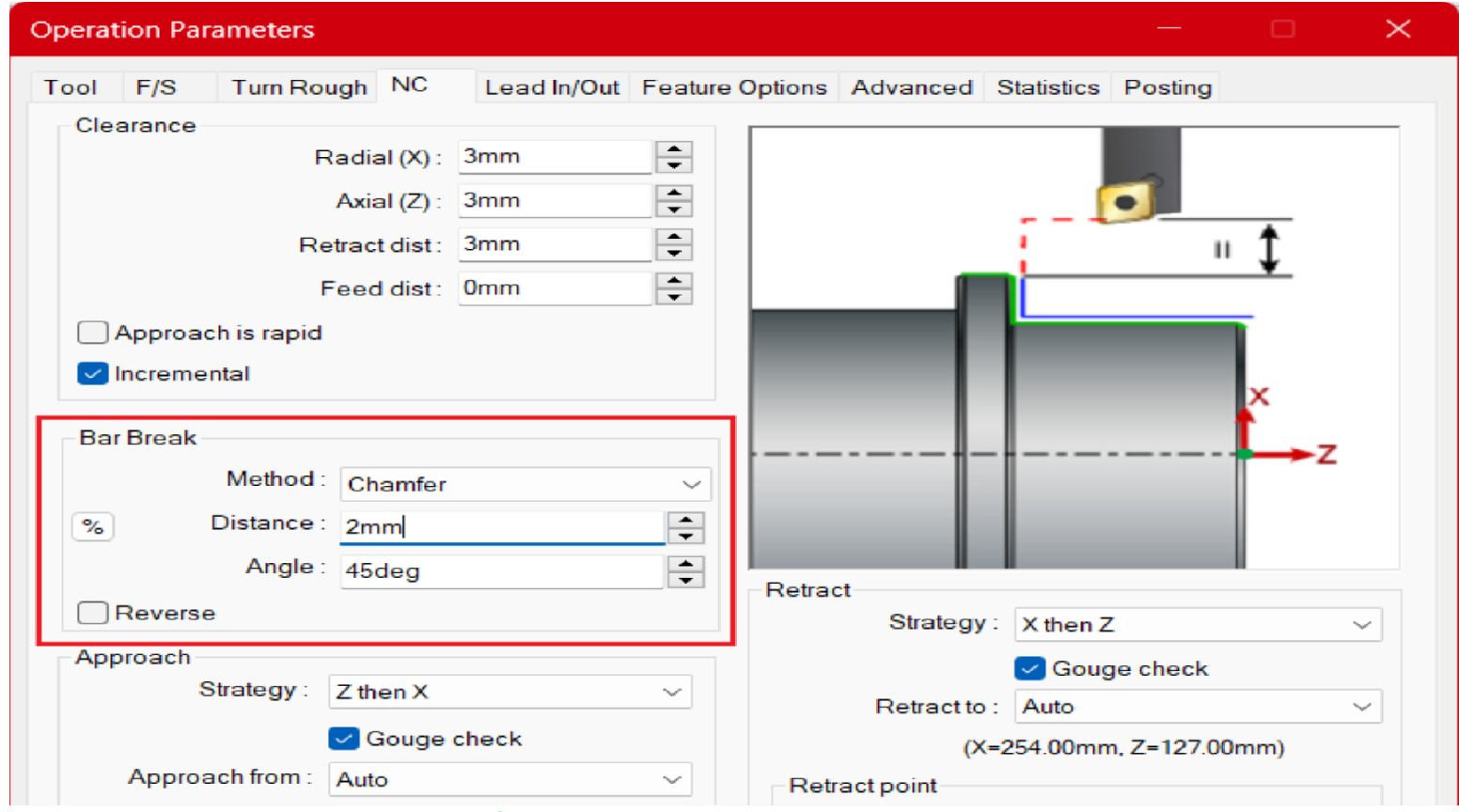
TechDB and Interface Enhancements
- Ability to highlight focused parameter dimensions in the tool image, making it easier to identify and read tool data
- Ability to resize the tool grid to make the tool image larger for ease of viewing
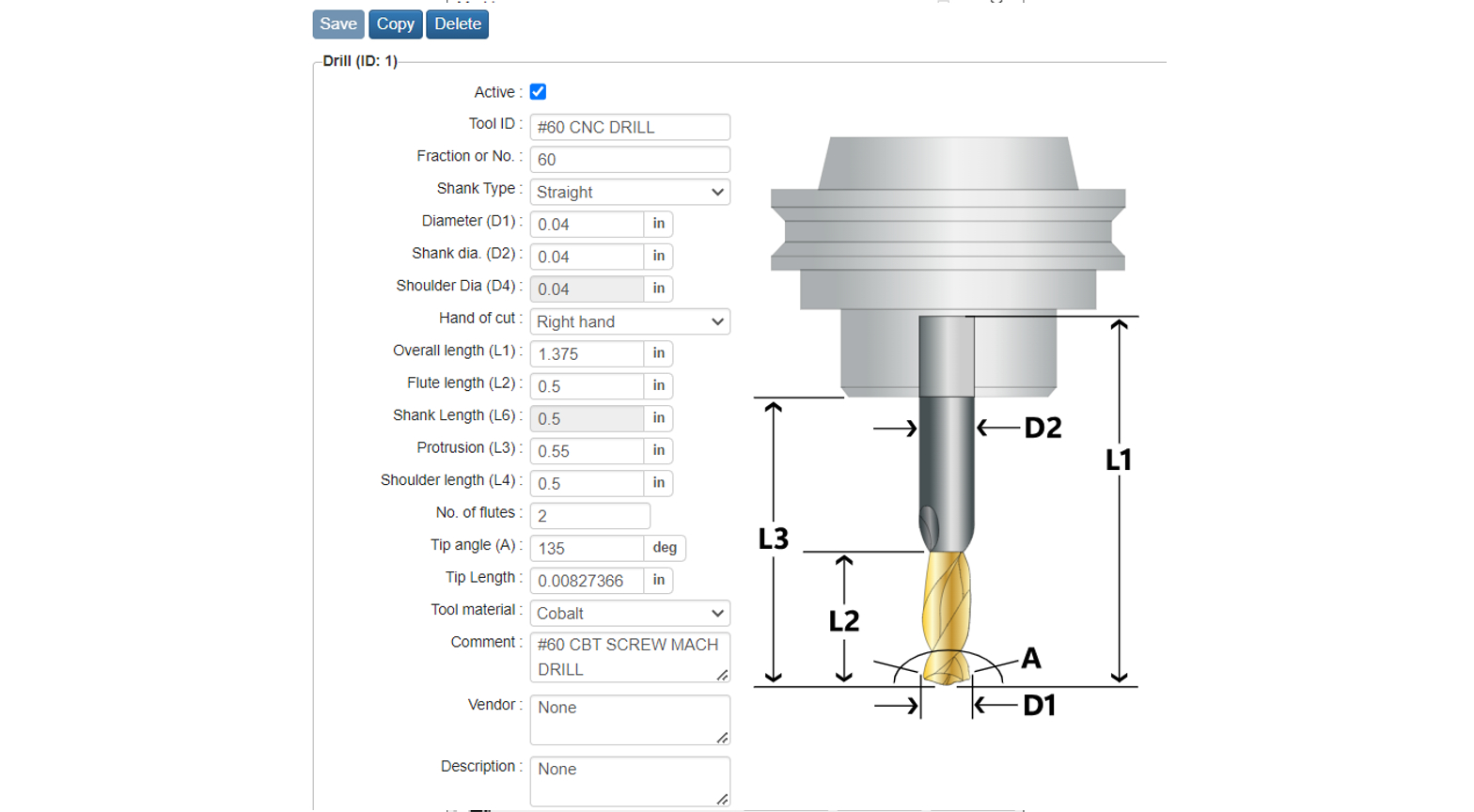