Accelerate Machining Productivity with HCL CAMWorks
- Reduces programming time through full integration with industry-leading CAD platforms such as SOLIDWORKS and Solid Edge
- Removes the need for multiple iterations between CAD and CAM systems with fully associative toolpaths that update automatically to design changes
- Eliminates repetitive programming tasks with feature-based machining and automatic feature recognition
- Streamlines programming and increases quality by capturing your shop’s best practices in a company-owned knowledge base to re-use in subsequent part programs
Digital Transformation using HCL CAMWORKS
Key Stats
50%
Cut Setup
Time
80%
Reduce Cycle
Time
400%
Increase
Production
500%
Increase
Tool Life
Why CAMWorks CAM Software ?
We are SOLIDWORKS Gold-level solution partner in CAM since 1998. CAMWorks is fully integrated with SOLIDWORKS.
Uses tolerances and features in 3D models to automatically create CNC programs
Automatic Feature Recognition (AFR) automatically recognizes over 20 types of prismatic features on native SolidWorks part models, reducing programing time by as much as 90% compared to traditional CAM software
Allows you to capture and reuse your programmers’ best practices using the patented TechDB, reducing programming time by as much as 80% and providing a company owned database to store employee knowledge and skill
Performs true G-code machine simulation directly from the G-code used for the CNC machine, eliminating dry runs and set up time
The ultra high-performance toolpath engine allows you to reduce your cycle time by 80% for complex 3D- shapes and prismatic parts
Seamlessly Integrated Inside SOLIDWORKS
As the first CAM solution to offer true knowledge-based machining capabilities, CAMWorks leads the way in advancements in Automatic Feature Recognition (AFR) and Interactive Feature Recognition (IFR). CAMWorks offers true associative machining - automatically accommodating changes to the part model. This means that any modifications made to the design are automatically updated in the CAM data, which eliminates time consuming CAM system rework due to design alterations.
Thanks to its seamless integration with SOLIDWORKS, CAMWorks allows you to:
- Use and manage just one file for both CAD and CAM systems.
- Use the CAMWorks machining tree and commands at the click of a button along with SOLIDWORKS, plus generate toolpaths without leaving the familiar SOLIDWORKS environment.
- Use the same SOLIDWORKS geometry to generate toolpaths to ensure the part machined is the same as the part that is modeled.
- Eliminate time-consuming file transfers using standard file formats such as IGES and STP.
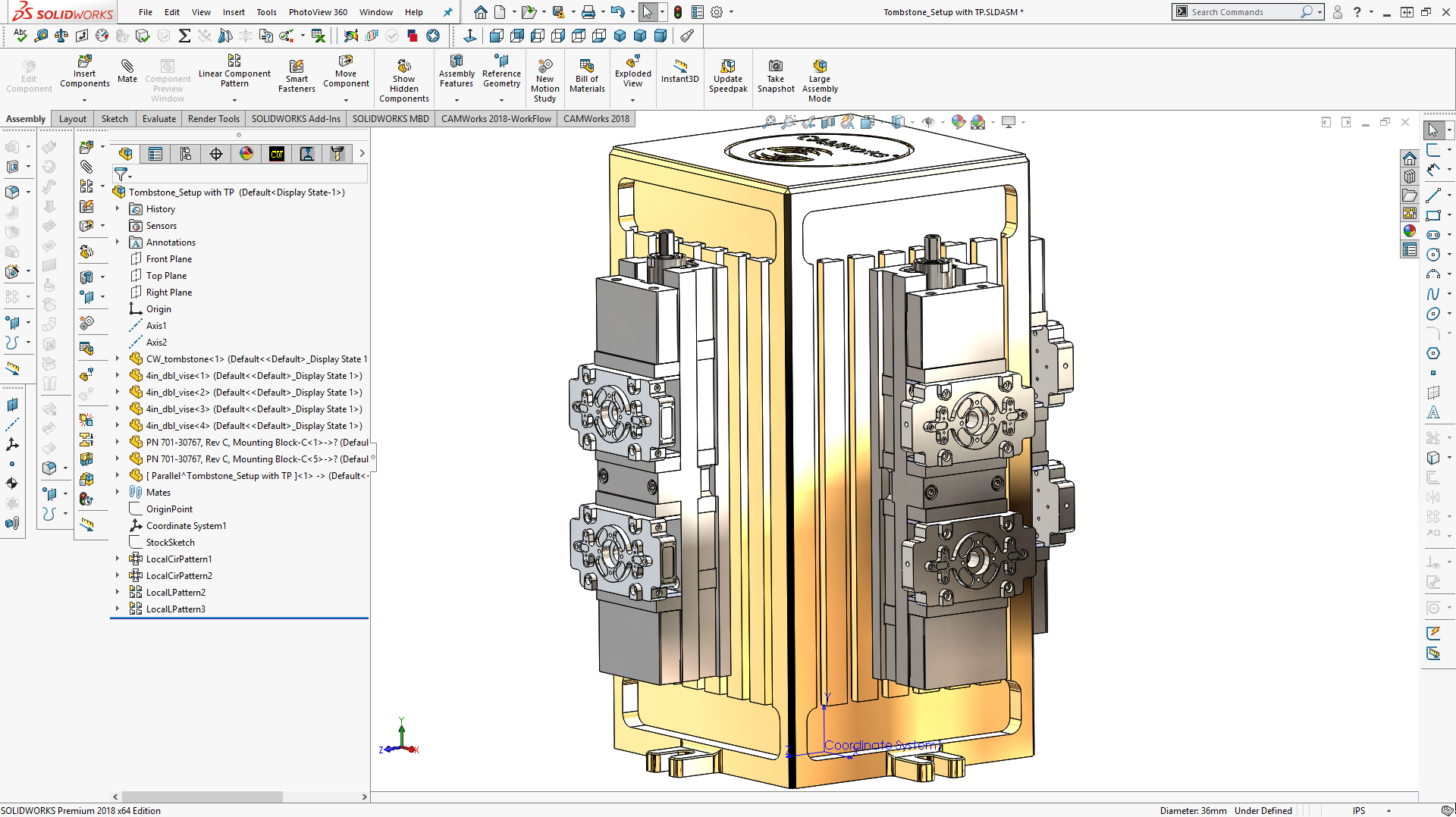
CAMWorks is the First SOLIDWORKS® Certified Gold Product for Manufacturing/CAM Software seamlessly integrated into the design software.
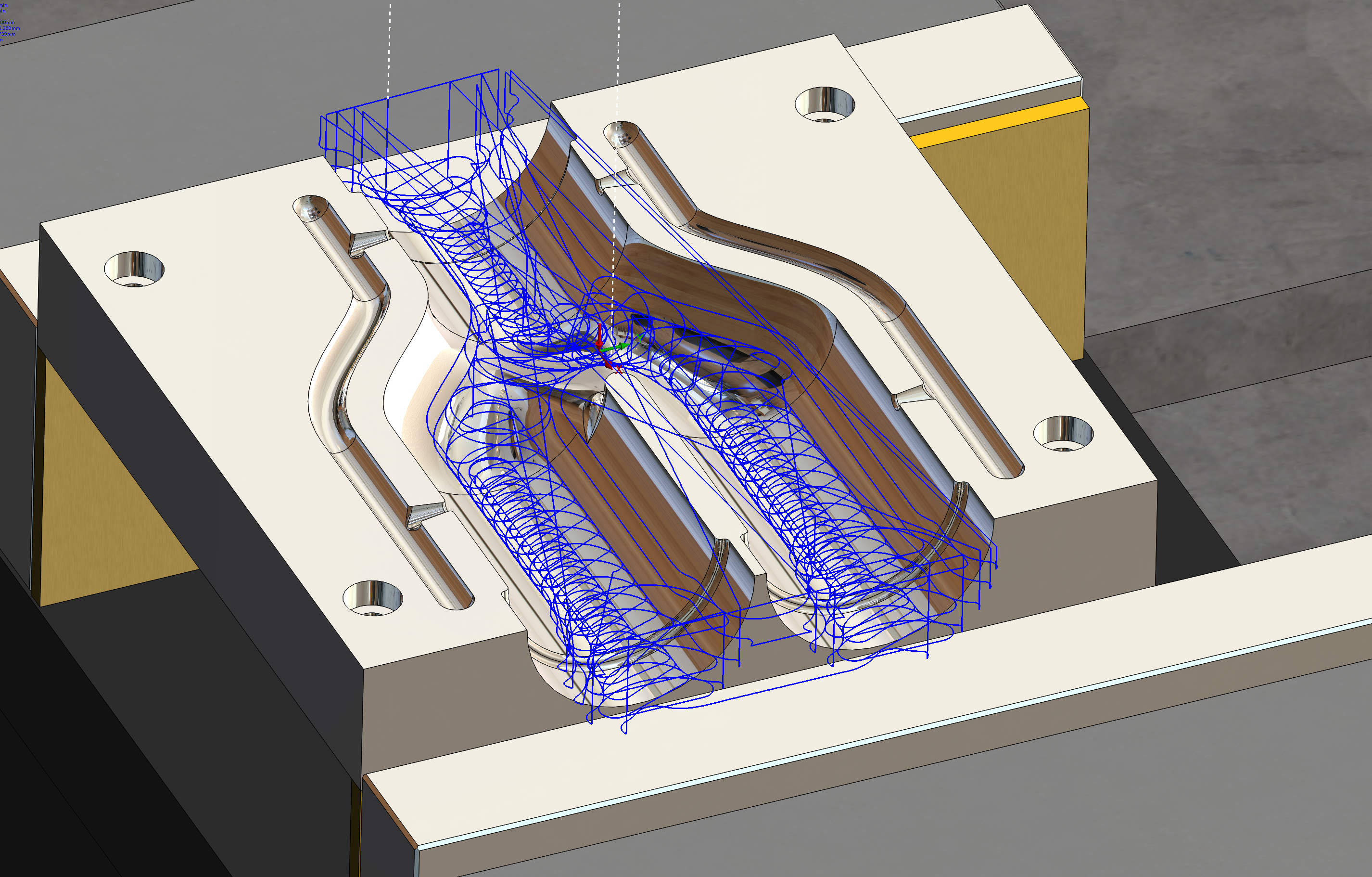
Ultra High-Performance Toolpath Engine within CAMWorks for 2.5 and 3 Axis Roughing Operations
Faster Cycle Times - CAMWorks® VoluMill
CAMWorks® VoluMill™ is ideal for complex 3-D shapes and prismatic parts as its algorithms result in more intelligent toolpaths to machine pockets, slots, and arbitrary shapes. VoluMill is well suited for machining soft as well as hard materials that are hard to chip, such as titanium, nickel-based alloys or stainless steel. The result is increased efficiency and utilization of machines, tools, labor and materials.
The high-performance roughing module, combines optimal milling paths and maximum material removal with minimized machining times. VoluMill’s unique approach to high speed material removal allows the programmer to determine the optimum material removal rate for any combination of part geometry, material, machine, and cutting tool..
- Reduce your Cycle Times up to 80%
- Reduce your programming times up to 50%
- Increase your Cutting Tool Life up to 500%
Cut Your Setup Time - CAMWorks® Virtual Machine
CAMWorks Virtual Machine uses the latest technology to perform true G-code machine simulation directly from the G-code used for the CNC machine. We are the first CAM software to bring true G-code machine simulation directly integrated within the CNC programming environment. Unlike other CAM systems that use cutter location (CL) data for machine simulation, CAMWorks Virtual Machine uses the actual G-code to ensure precision and accuracy.
- Cut Setup Times by 50% or more
- True G-code Machine Simulation
- Full Collision Detection - including the tool, tool holder, machine components, and fixture
- Avoid Collisions and Broken Tools
- Reduce Maintenance Costs
- Extend Machine Life
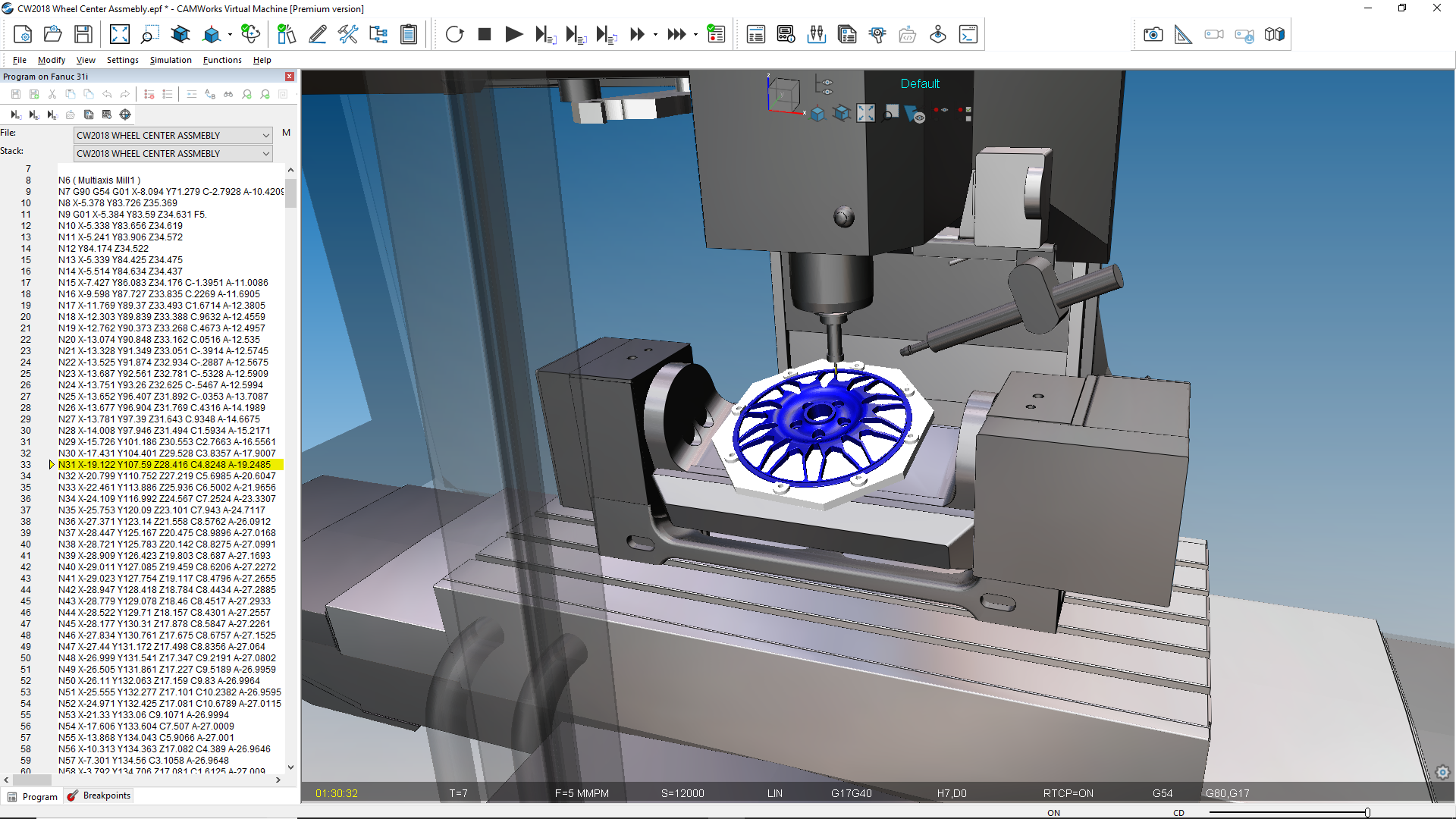
Verify G-Code With 1 Click. With CAMWorks Virtual Machine, dry-runs for program validations are completely eliminated.
Modern Toolpath Generation for your SOLIDWORKS Designs
Tolerance Based Machining (TBM)
With the introduction of Tolerance Based Machining by CAMWorks, the manual tasks associated to preparing parts with close tolerances, asymmetric tolerances, surface finishes and other drawing annotations for toolpath generation will now be part of the past. Not only does CAMWorks automatically identify manufacturing features and automatically create toolpaths, CAMWorks will now recognize the tolerances and surface finishes associated with a feature to select the appropriate tools, speeds, feeds, etc… to generate the best toolpath. For the first time, an application that leverages this information to automate and dramatically accelerate the manufacturing process is now available.
- Reads SOLIDWORKS® MBD/DimXpert dimensions and surface finishes
- Automatically selects machining strategies to meet the specified tolerances
Our Clients
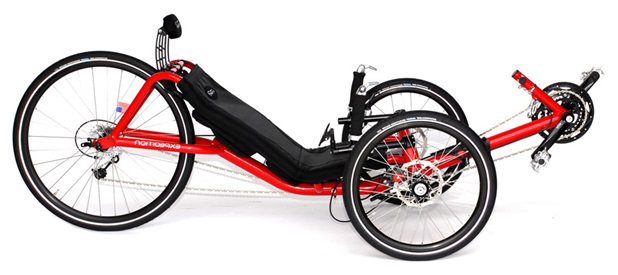
“If you're designing in SOLIDWORKS and you want to start machining, get CAMWorks.”
- Lynn Bradbury, Catrike
Catrike was created in 2000 and has earned numerous awards along the way. Their focus on product development, engineering and process design has made for great, user-friendly trikes that not only look cool, but perform beautifully with little maintenance.