What is CAD and CAM Software?
Computer aided design (CAD) and computer aided manufacture (CAM) both refer to software used to aid in design and machining in the manufacturing industry.
CAD software, typically used by engineers and designers, aims to improve design efficiency, quality, and communication across departments and functions through precision digitized design. Because CAD software can output design to commonly accessible files, it is useful for product copyright and patent filing. Engineers, architects, and designers use CAD software for 2D and 3D part and whole product design. CAD software replaced drafting by hand, which was particularly important for aircraft, ships, vehicles, and other large industrial design. A limited amount of CAD functionality is often part of CAM software systems. However, to utilize the advanced functionality in full CAD systems, products are more often designed in the CAD system and then exported via a STL file or equivalent into the CAM system.
CAM software is used by CNC programmers and machinists to generate the toolpaths and G-code needed to machine the parts on CNC machines. Both CAD and CAM software are integral to ensuring precise processing, faster and less costly production, and reduced rework in the manufacturing stage when it is far costlier to correct errors.
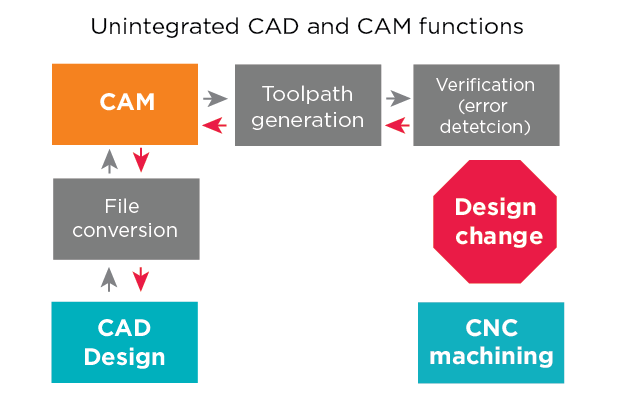
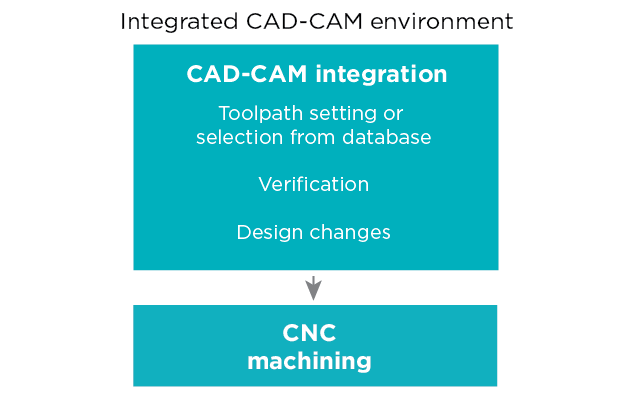
What is a CAD CAM Integrated Software?
CAD and CAM software outputs to 2D and 3D models and is used to manufacture parts with CNC machines. CNC (Computer Numerical Control) machining utilizes computers to control machine tools such as lathes, mills, routers and grinders.
When CAD and CAM software are not fully integrated, potential costs and delays are introduced because a handoff and back and forth iteration of design and correction exists. Without integration, importing a design into production may require translation or conversion, which introduces the possibility of errors. Programming tool paths becomes a time-consuming process that must be recreated each time. Often issues with design, material cost or sourcing, and manufacturability go undetected until the part or product is ready for tooling or deep in the manufacturing process if multiple parts require tooling for the whole product, which results in costly rework. Any time a change is required, the same back and forth iterative process begins again. Inaccuracy, lost time, high costs of single-source material, scrapped material, and poor communication across teams are big drivers to integrate CAD and CAM functions.
The advantages of integrating CAD and CAM functions are regarded as significant. In most companies, design and manufacturing teams operate separately, and changes between the teams require time-consuming, back and forth iteration. Combining CAD and CAM allows seamless automated file translation from CAD to CAM. Fully integrated CAD CAM software refers to CAD and CAM systems that work from the same model design data. Instead of design model information being exported from the CAD system and then imported into a separate CAM system, often resulting in translation errors or data loss, fully integrated CAD CAM systems remove the need to translate the part model data. Integrating CAD with CAM software helps unify a design throughout the manufacturing process. An integrated CAD CAM platform creates a collaborative process with more efficient and cost effective activities, much earlier in the process. The single model of supporting both design and manufacturing functions in a CAD CAM system improves the likelihood of product manufacturing meeting budget and timeline.
How Does CAD CAM software work?
Engineers use CAD to create 2D and 3D part shapes using points, lines, circles, and other simple shapes. The software can create surfaces such as 3D contours that then define a shape. Modern CAD software can design parts used in 2, 3, 4, and 5 axis CNC machining, which is then transferred to CAM for programming for the machine side of the manufacturing process. The language handling this output is called G-code. To turn a CAD design into a usable file using G-code, CAM software identifies the cutting path and speed of the cut to feed the part. CAM software allows the ability to input tool data or choose from a library or existing ones, and save custom toolpaths for reuse. Toolpaths can have several layers of detail such as hole drilling, profiling, engraving, facing, and contouring.
Integrated CAD CAM software uses CAD as its front-end, geometry engine. An integrated CAD CAM platform performs CAM operations on the CAD file itself without having to import or convert. With integrated CAD CAM software, design and manufacturing engineers can work from the same model. Design changes and updates are automatically dispersed to related tool paths and drawing, automating any updates or changes. Integrated software, such as HCL CAMWorks, can automatically search for parts availability or optimization based on automatically communicated changes.
Additional opportunities in an integrated CAD CAM environment include leveraging toolpaths and design tables to drive multiple production configurations or APIs to automate functions.
CAD CAM Use Cases
Several industries rely on a high degree of accuracy and precision in product or part manufacturing particularly benefit from CAD CAM integrated software. These include aerospace (including aircraft, satellite, and missiles), and automotive, where design accuracy and communication can affect lives. With complicated, high-stakes manufacturing, using CAD CAM integrated software allows designers to visualize details before the product is built, thereby correcting issues before manufacturing begins.
Other industries include dentistry, which utilizes CAD CAM to digitize dental structures, a previously manual and often inaccurate process. Clothing design uses the CAD CAM environment to ensure consistency across mass-production of cuts and patterns. Smaller businesses that produce specialty products or parts benefit from automating a process that would require the employment of several more specialized personnel, which may not always be possible.
Benefits of CAD CAM integrated software for organizations
- Smaller contract manufacturers that provide precision machined parts to larger clients in aerospace, telecommunications, military, and medical industries find the integration of CAD CAM platforms beneficial. Those include HCL CAMWorks with SOLIDWORKS and other third-party systems, as well as a host of APIs (application programming interfaces) that further enhance interoperability.
- Toolpath simulation and a technology database allow users to capture and reuse best programming practices, this providing a high degree of automation on a smaller scale.
- A technology database can reduce machining time by as much as 80%. This gives independent shops the ability to retain a high degree of competitive edge over other shops of similar scale by programming smarter and machining faster.