Over the past 10 years, productivity from the manufacturing industry has increased 1.2% compared to 2.6% from the previous 7 years. But new emerging technology trends are disrupting the way engineering companies design, manufacture, and deliver products. There is a need for increased innovation to ensure that products are differentiated, allowing you and your teams to compete in an increasingly competitive environment.
In the past product design and manufacturing groups typically operated as separate, disconnected functions resulting in lots of late stage engineering changes, affecting product cost, quality and time to market. Once the design is completed and handed over to manufacturing, because of the standalone applications use by these departments, there is a need of data imports, translations, and conversions. Also, any changes required to design because of manufacturability issues would mean design and manufacturing need to repeat above process once again to finish up the production.
Integrated CAD/CAM offers a bridge between design and manufacturing teams and gives the user complete control over the whole design and manufacturing process. An integrated CAD/CAM environment is a critical factor in helping to ensure the users can benefit from solids-based, fully associative CNC machining, whether it's with native solid models or neutral file formats like IGES, STEP, etc. With a completely integrated solution users can make the design changes easily and toolpaths will automatically adapt themselves.
Request demo
“If you're designing in SOLIDWORKS and you want to start machining, get #CAMWorks.”
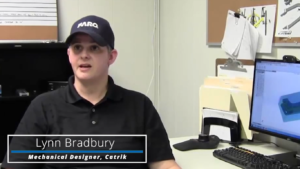
Decimal Engineering automates machining with CAMWorks, adds remote programming, data access with CAMWorks ShopFloor
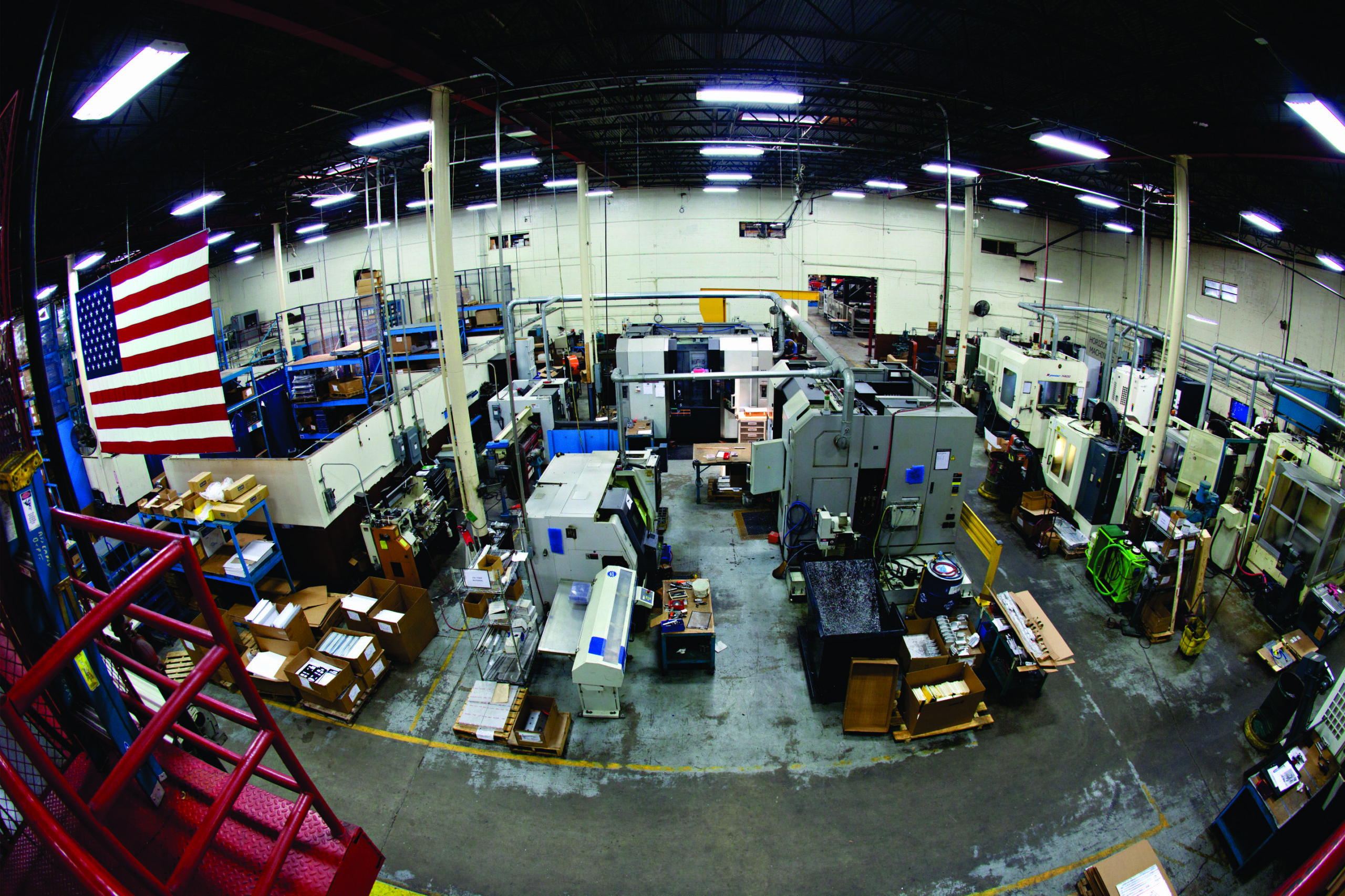
“With CAMWorks, it’s much easier to make a design change, and have the change automatically reflect in the manufacturing model. The software is more efficient—something what took 20 mouse clicks in our previous CAM software takes about five mouse clicks with CAMWorks—and because CAMWorks uses SOLIDWORKS as its modeling front end, all changes are captured and reflected in our engineering model. None of the modifications are lost, which leads to fewer mistakes”
5 Reasons to switch to integrated CAD/CAM
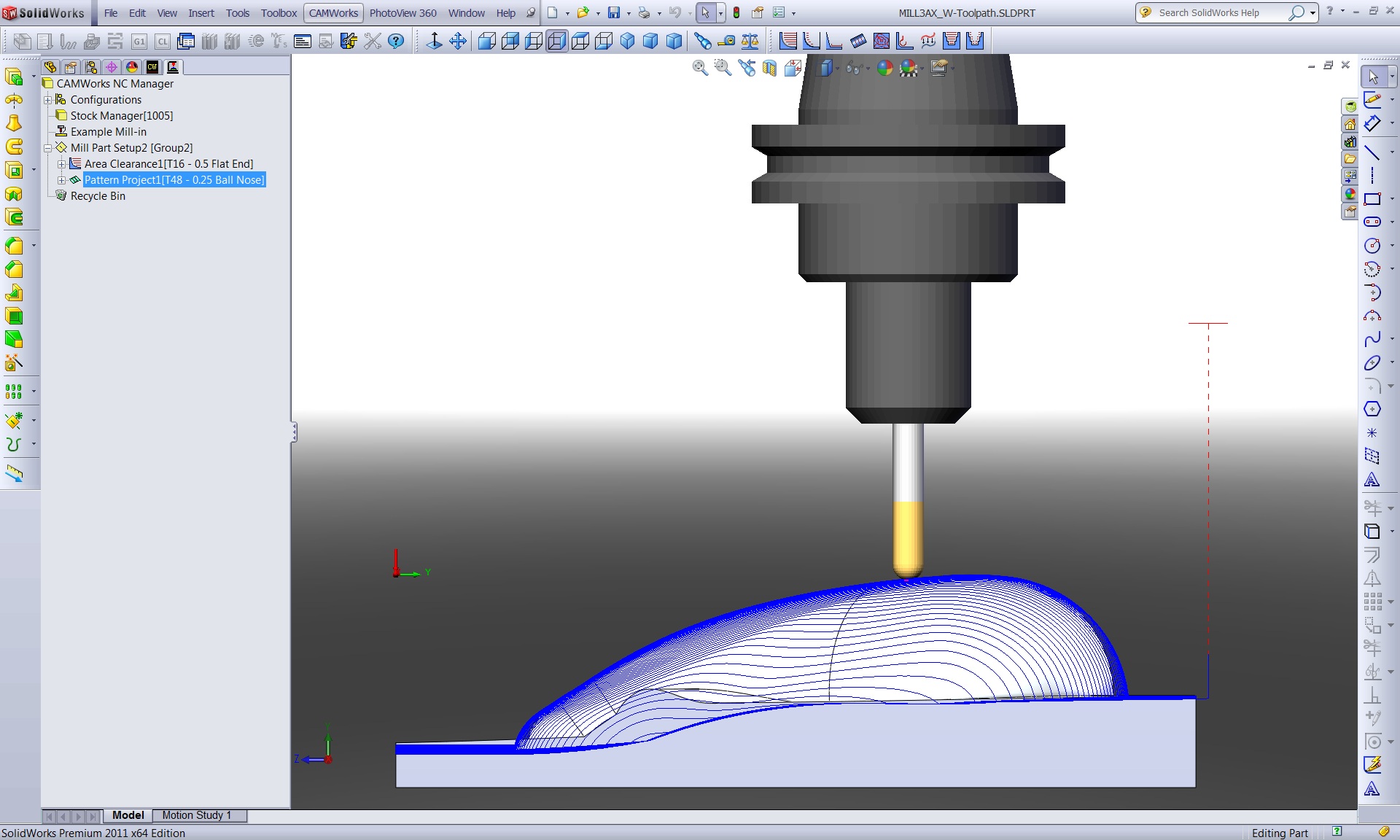
Integrated CAD/CAM helps to collaborate better between design and manufacturing departments and share knowledge so that designs can be done right the first time by considering the late-stage manufacturability issues upfront at the design stage. Addressing designs for manufacturability requirements is essential to meet program schedules, achieving high quality, reducing errors and rework, and controlling manufacturing costs. Let’s look at five major benefits integrated CAD/CAM systems can offer:
- Eliminate CAD and data translation errors
- Stay organized (avoid multiples disconnected file to maintain)
- Simplified workflow
- Automate the manufacturing processes
- Integrated validation tools
SOLIDWORKS and CAMWorks - a winning combination for designing championship air arms
“Its all about making a better-looking product and with SolidWorks working with CAMWorks the possibility of achieving this is greatly enhanced, whilst at the same time greatly reducing time to market.”
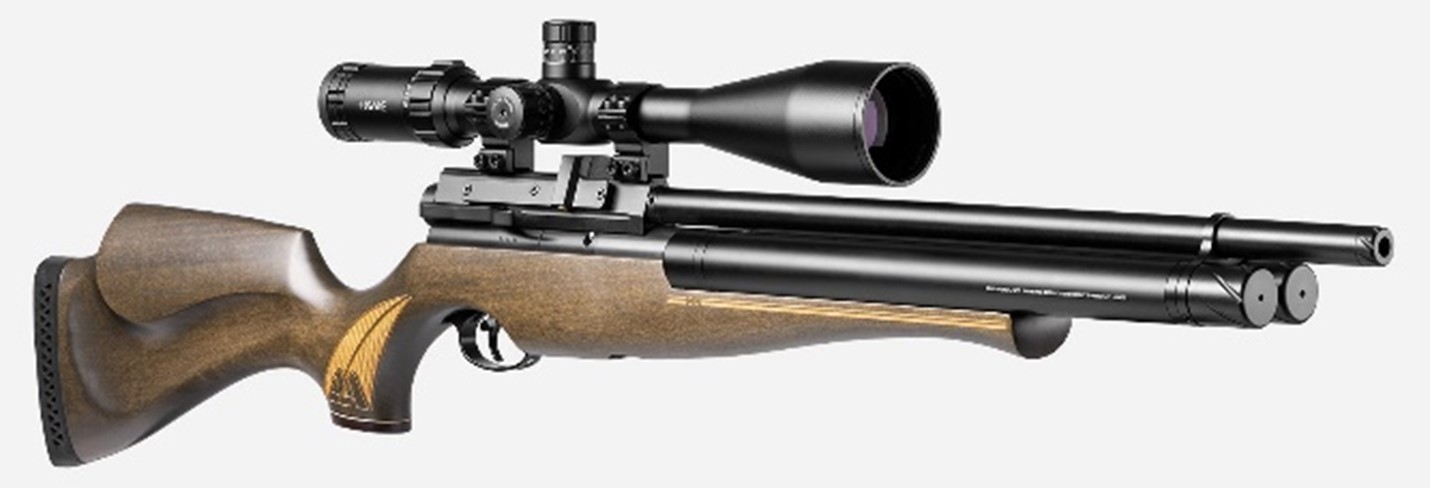
Affordable integrated CAD CAM for small machine shops
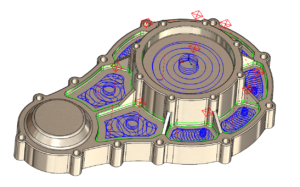
CAMWorks enables CP-Carrillo LLC to Optimize Programming and Business Processes
CP-Carillo, a leader in the production of pistons and rods for the power-sports and motor-sports racing industries, is leveraging the Applications Programming Interfaces (APIs) of the integrated SOLIDWORKS CAD and CAMWorks CAM solution to fully automate the design and part programming of its products.
When an order is received, technical sales personnel enter the specifications in an interface created with the SOLIDWORKS and CAMWorks APIs. Once the specifications for the model are entered, the software automatically generates the design model and tool paths for the part, which are then machined following a quick check. This integrated, automated approach reduces overall lead time by 85 percent, including a 95 percent reduction in design time, a 75 percent drop in CNC programming time, and a 20 percent decrease in scrap and rework.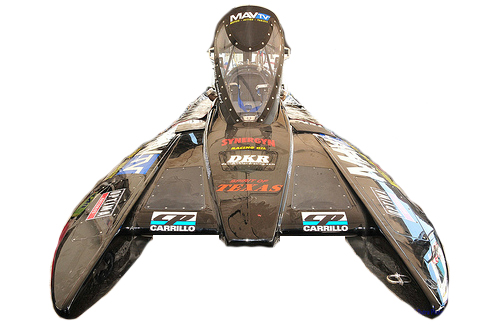